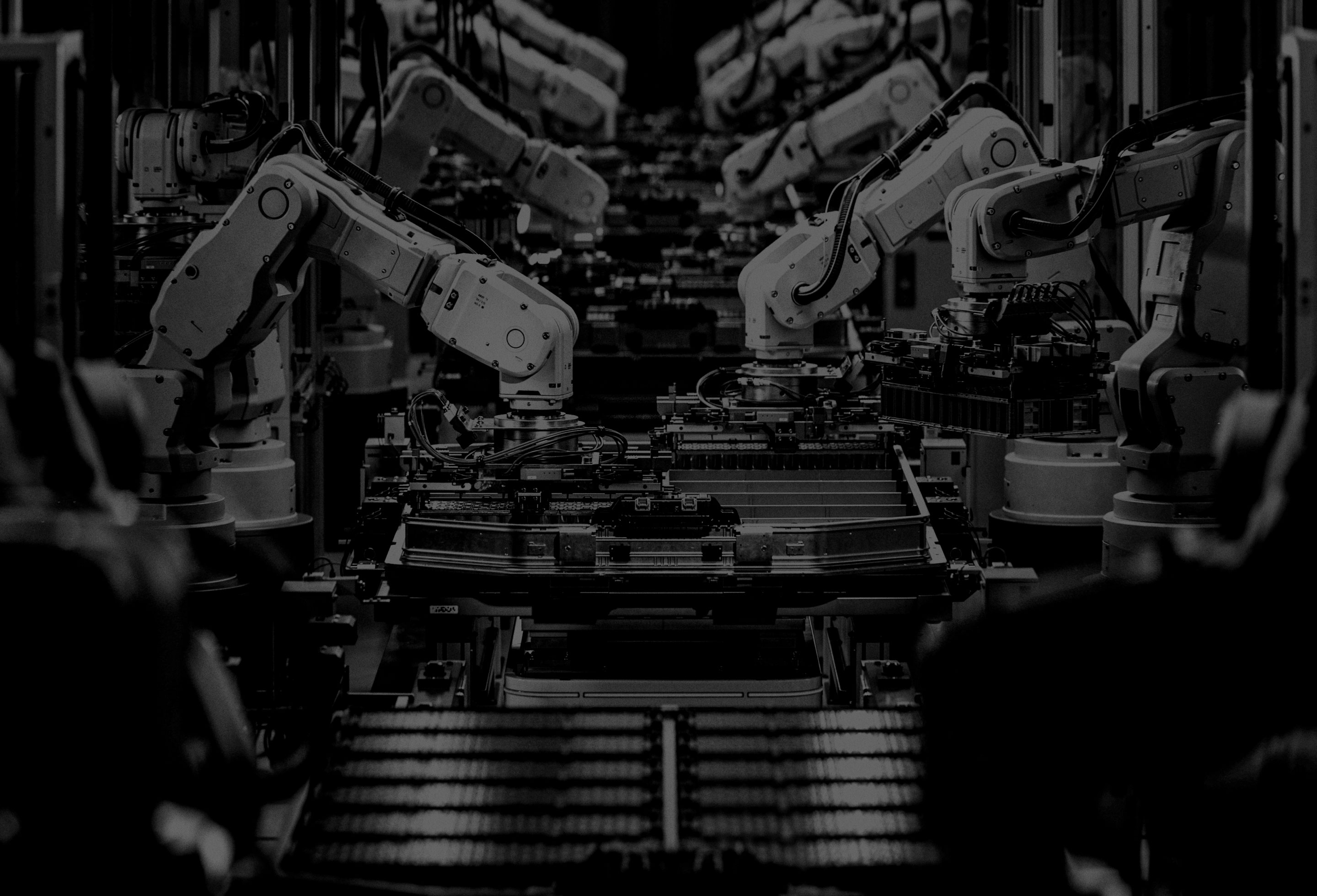
AND OUR
STRENGTHS
One of the unique strengths that Hokuto offers with confidence is what we call “full-turnkey” management. Through this approach, we build comprehensive, automated production systems that extend from engineering and design to manufacturing and body quality assurance. In recent years, we have introduced virtual commissioning technology to implement the “digital twin” concept as we continue to innovate our products and services, including by reducing delivery times.
Realizing peace of mind and efficiency
with “full-turnkey” management
“Full-turnkey” management is a project management approach in which all processes are handled comprehensively by a single provider. At Hokuto, we manage every stage of a project, from engineering and specification reviews to design, manufacturing, line setup, test runs, and final product quality refinement.
In other words, we take responsibility for all processes up to the point where customers can “turn the key” and immediately begin operations. Our proprietary technology and integrated production system enable us to achieve consistent quality, shorter delivery times, and lower costs.
and low costs through streamlined, high-efficiency operations
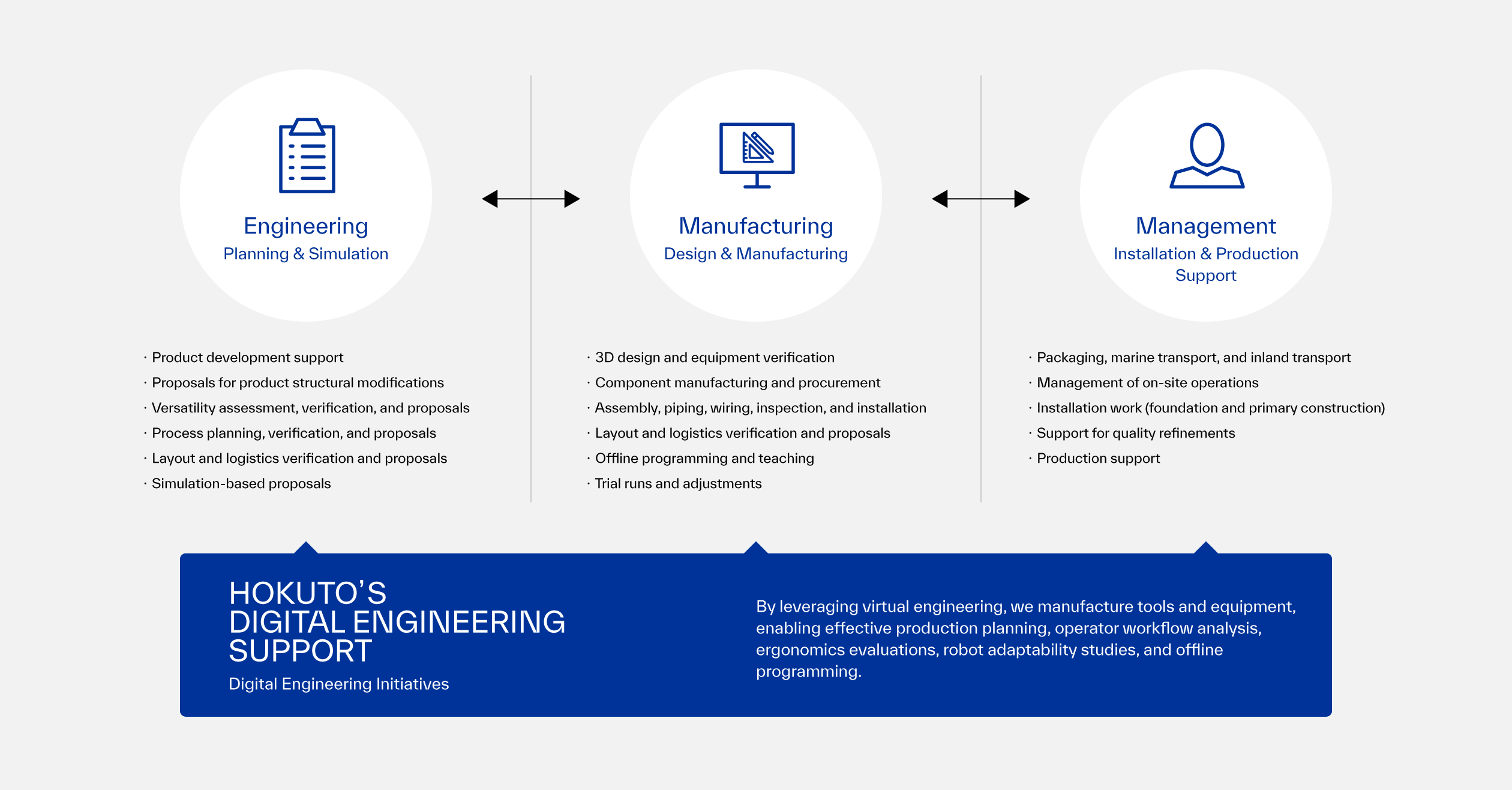
Verification capabilities using
virtual commissioning
Virtual commissioning is a technology that forms part of the “digital twin” concept, allowing for pre-operation verification in a virtual environment before constructing an actual production line. This technology enables real-time operation checks by connecting simulators to actual machinery and control systems like PLCs.
As the shift toward EVs in the mobility market brings significant changes to manufacturing, Hokuto leverages cutting-edge technology to identify and resolve various issues, contributing to the early operational startup of our customers’ factories.
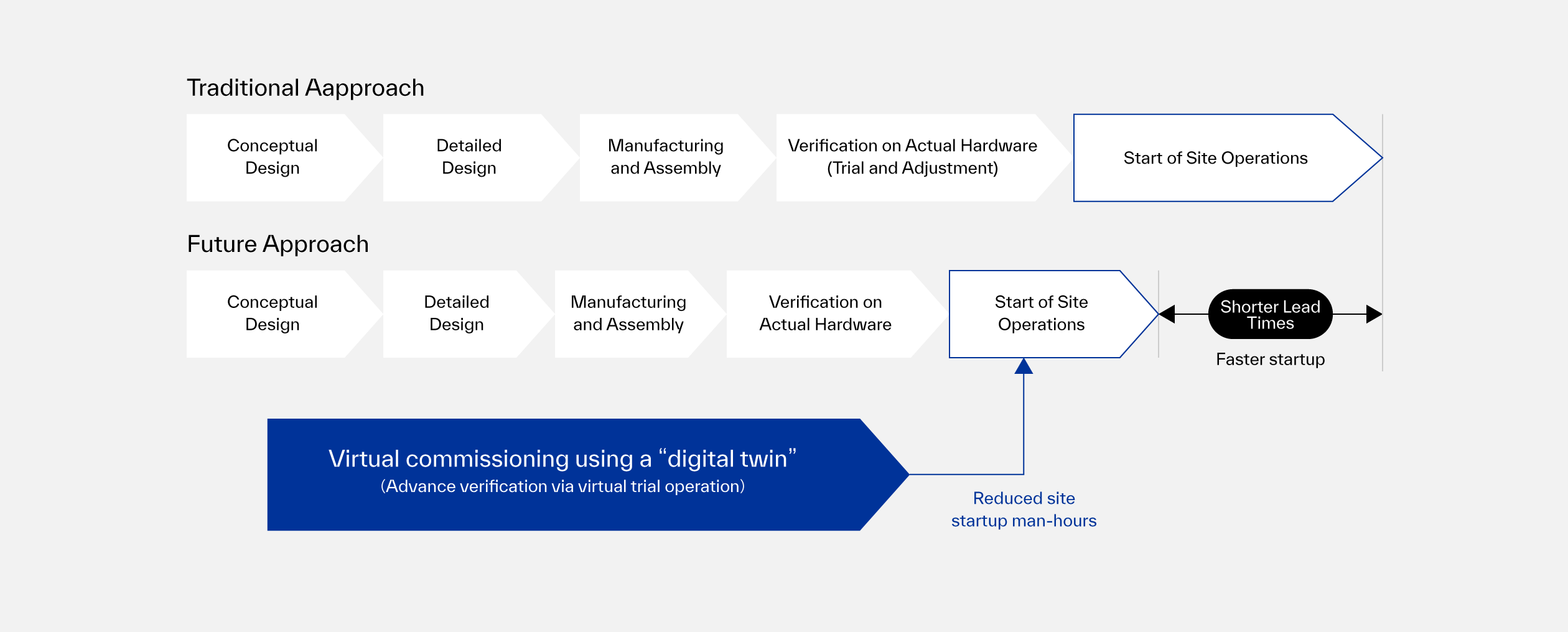
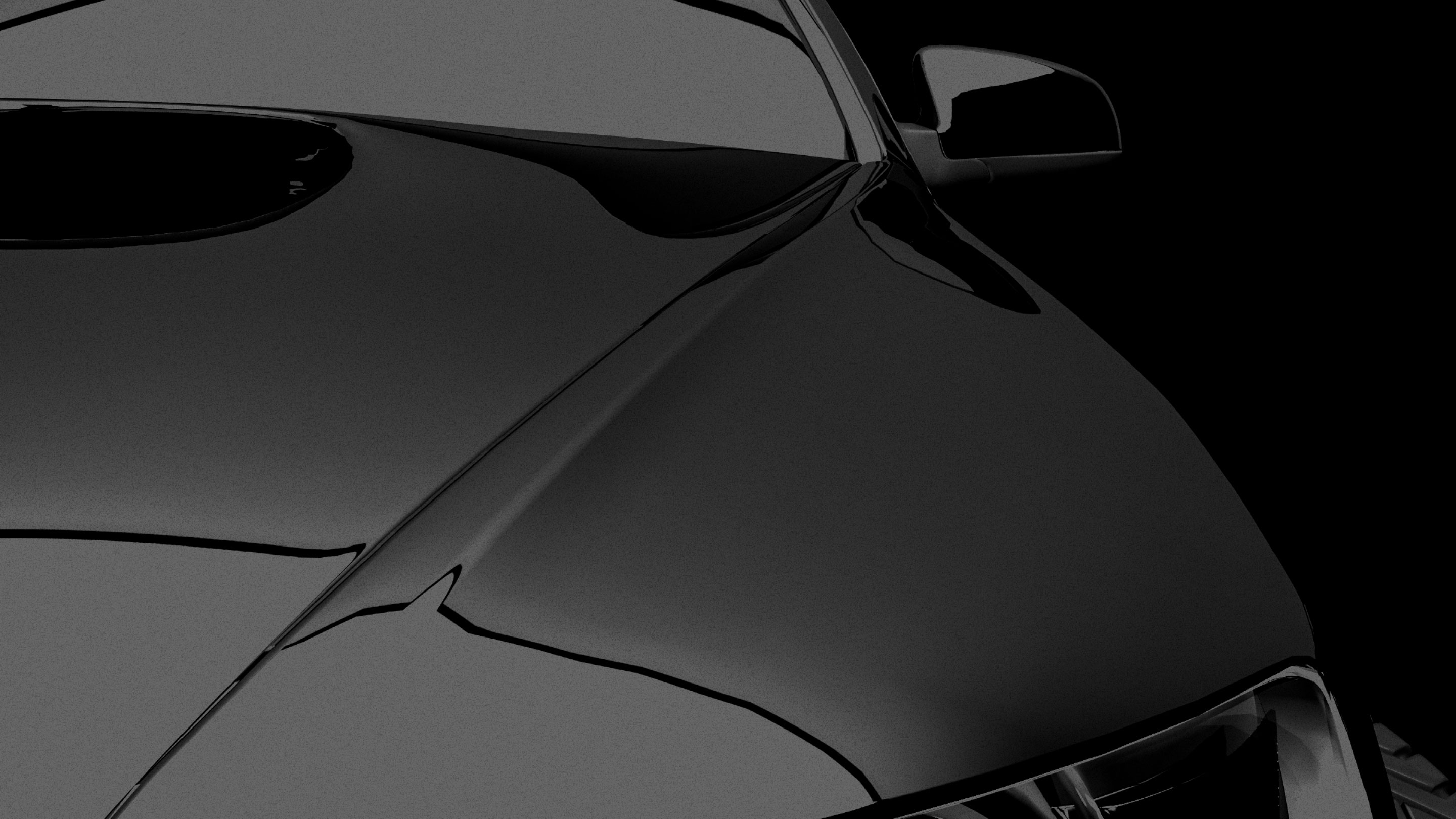
Automotive Body Manufacturing
Of the various processes involved in assembling automotive bodies, including pressing, welding, painting, and assembly, Hokuto specializes in welding and assembly lines, conveyor systems and hemming presses.
Welding and Assembly Lines
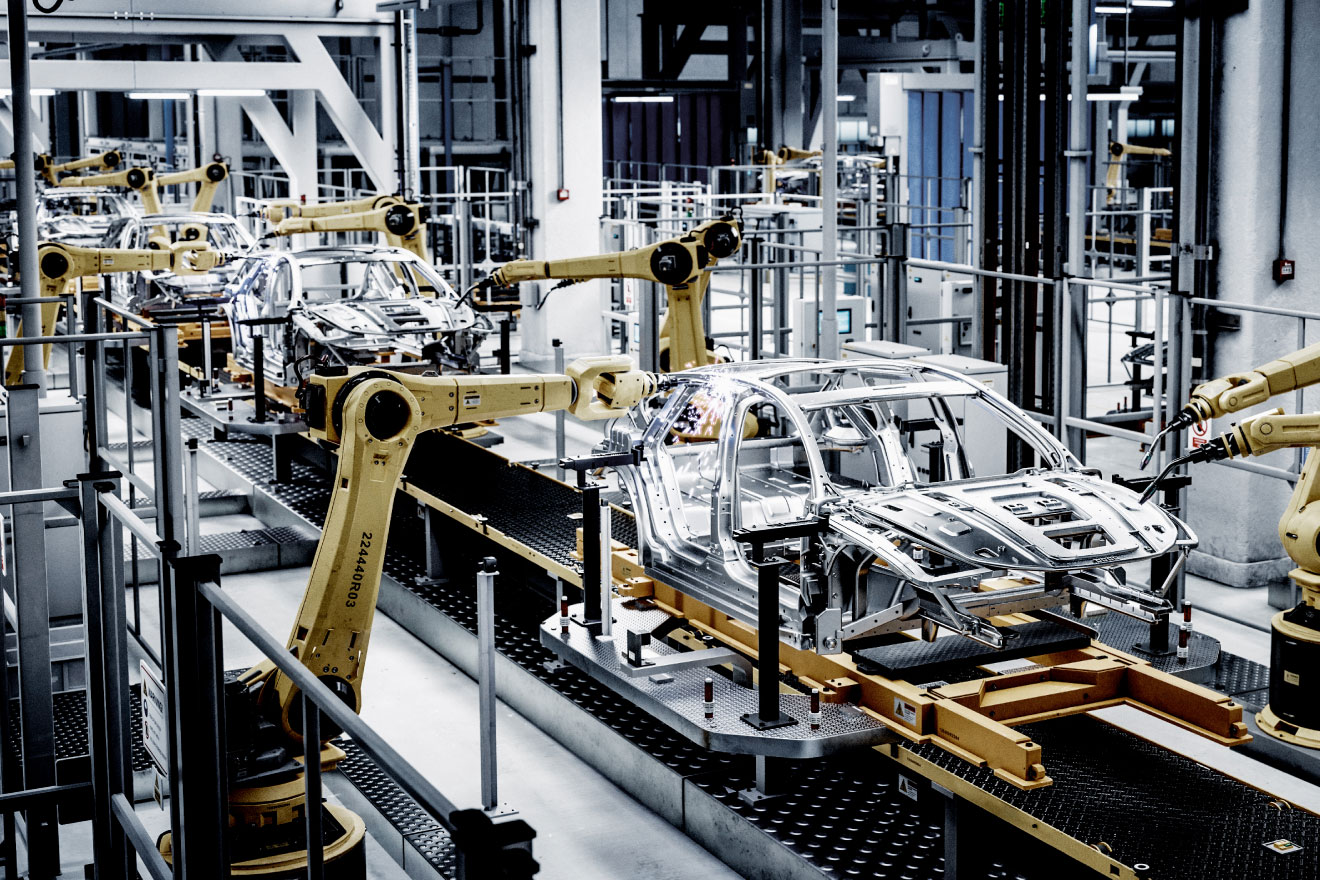
The manufacturing of automotive bodies involves multiple processes, including pressing, welding, painting, and assembly. In the welding process, multiple robots use welding guns to apply electrical current, bonding parts together with electrical force and assembling the vehicle’s framework. Hokuto designs and constructs these production lines with proprietary technology, enabling the production of over one vehicle per minute with tens to hundreds of robots.
Conveyor Systems
To achieve efficient manufacturing processes, automotive body production plants utilize various types of conveyor systems. These systems span dozens of types based on factors such as conveyance speed, positioning accuracy, and drive mechanism. Leveraging extensive experience ranging from gravity conveyors to multi-axis robotic conveyor systems, Hokuto provides optimized conveyor system solutions tailored to customer needs.
Hemming Presses
Hemming presses are used to perform hemming (metal bending and joining) for doors, hoods, and trunk lids, collectively known as automotive closures. Hokuto offers a wide range of hemming presses to meet diverse customer requirements.
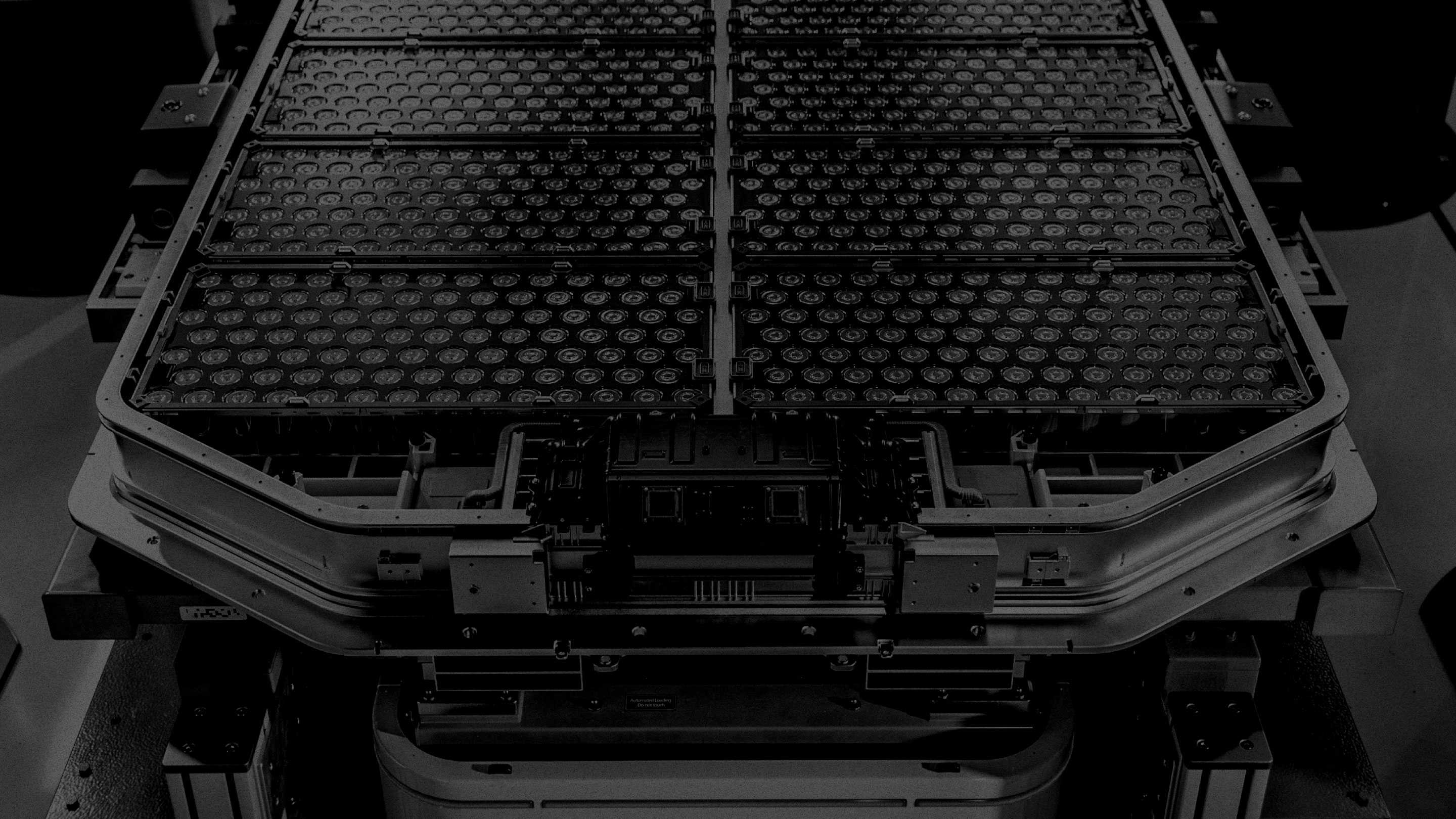
EV Battery Solutions
Against the backdrop of the decarbonization megatrend in the mobility market, demand for automotive storage batteries (EV batteries) continues to grow.
Automated Production Equipment
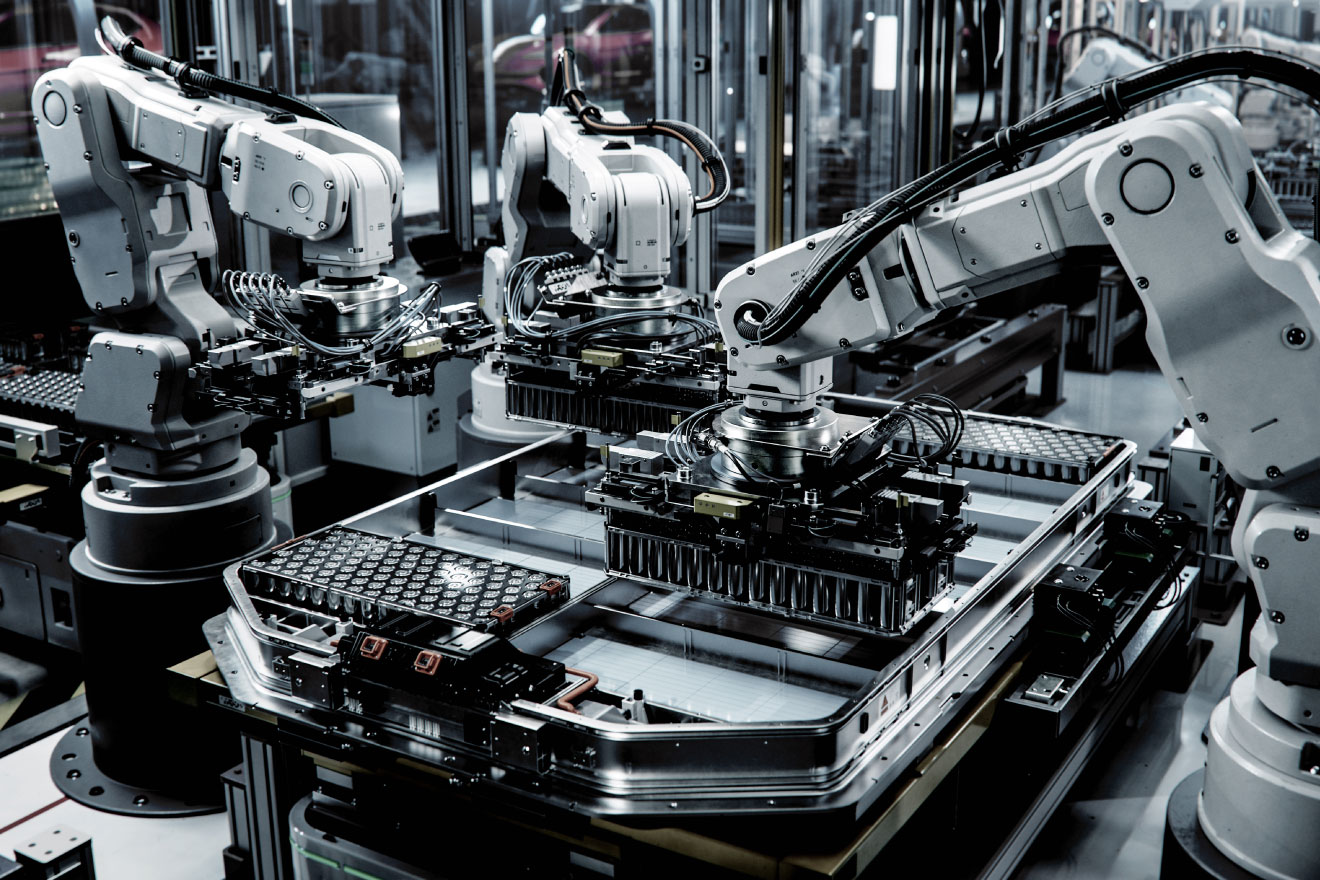
Automotive storage batteries are manufactured through multiple processes. Leveraging the expertise developed through automotive body production lines, Hokuto provides automated production equipment that enables efficient EV battery manufacturing processes.

General Industry and Aerospace
By utilizing automation technologies developed in connection with our work on automotive body production lines, Hokuto develops proprietary automated production systems and proposes efficient production equipment for use in a wide range of industries. We also develop and propose processes for not only existing products, but also products still in the research and development phase. We supply production systems tailored to customers’ needs, including robot-based automation systems and systems that integrate various types of automation equipment.
Aerospace
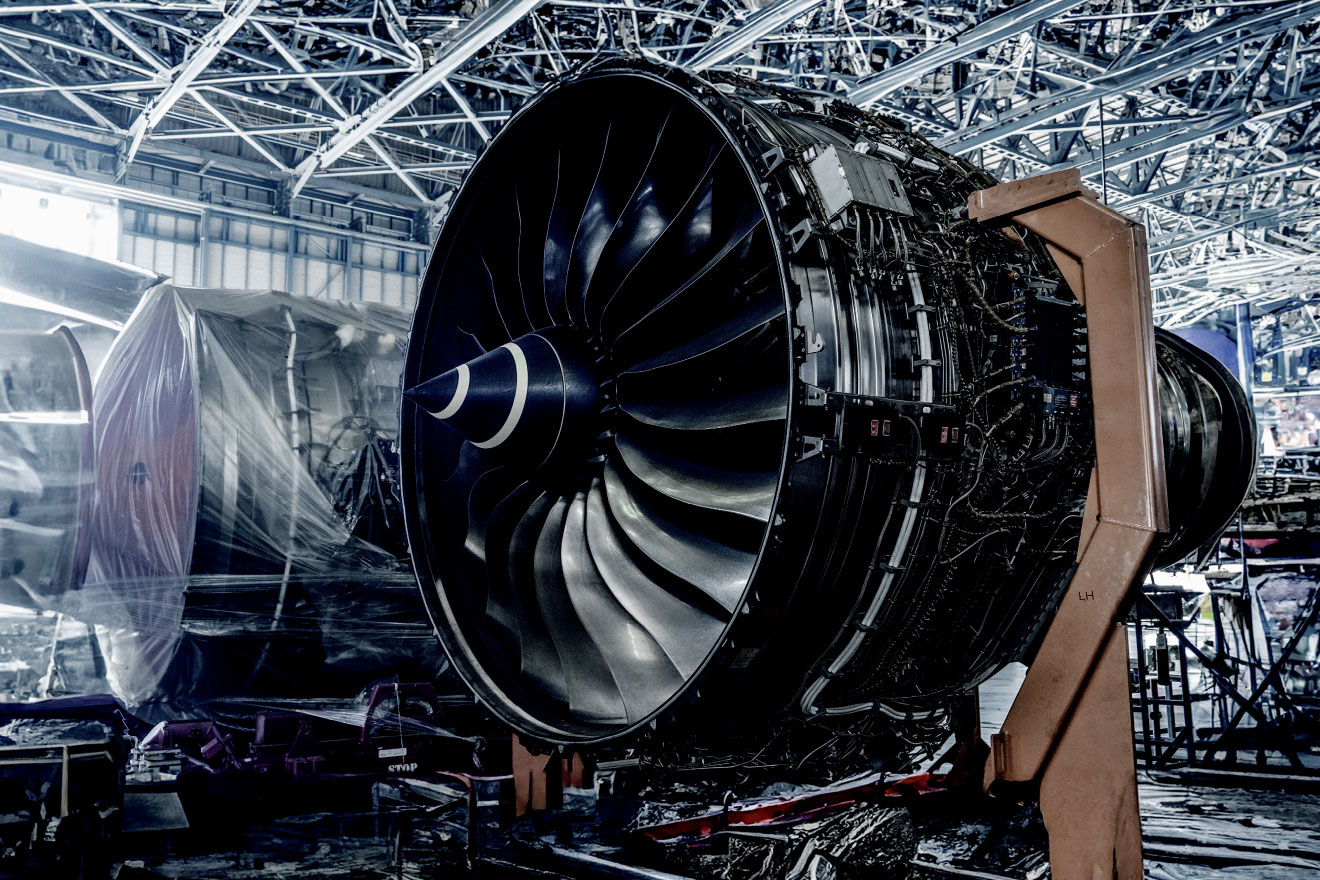
Demand for aircraft, which are central to logistics and transportation, is expected to grow over the medium to long term. In addition, compared to the automotive industry, the aerospace industry is characterized by use of a larger number of parts and more pronounced technological spillover effects. Through its unique production systems, Hokuto supports the development of Japan’s aerospace industry from its base in the Tokai region, which serves as a hub for the aerospace sector.
General Industry
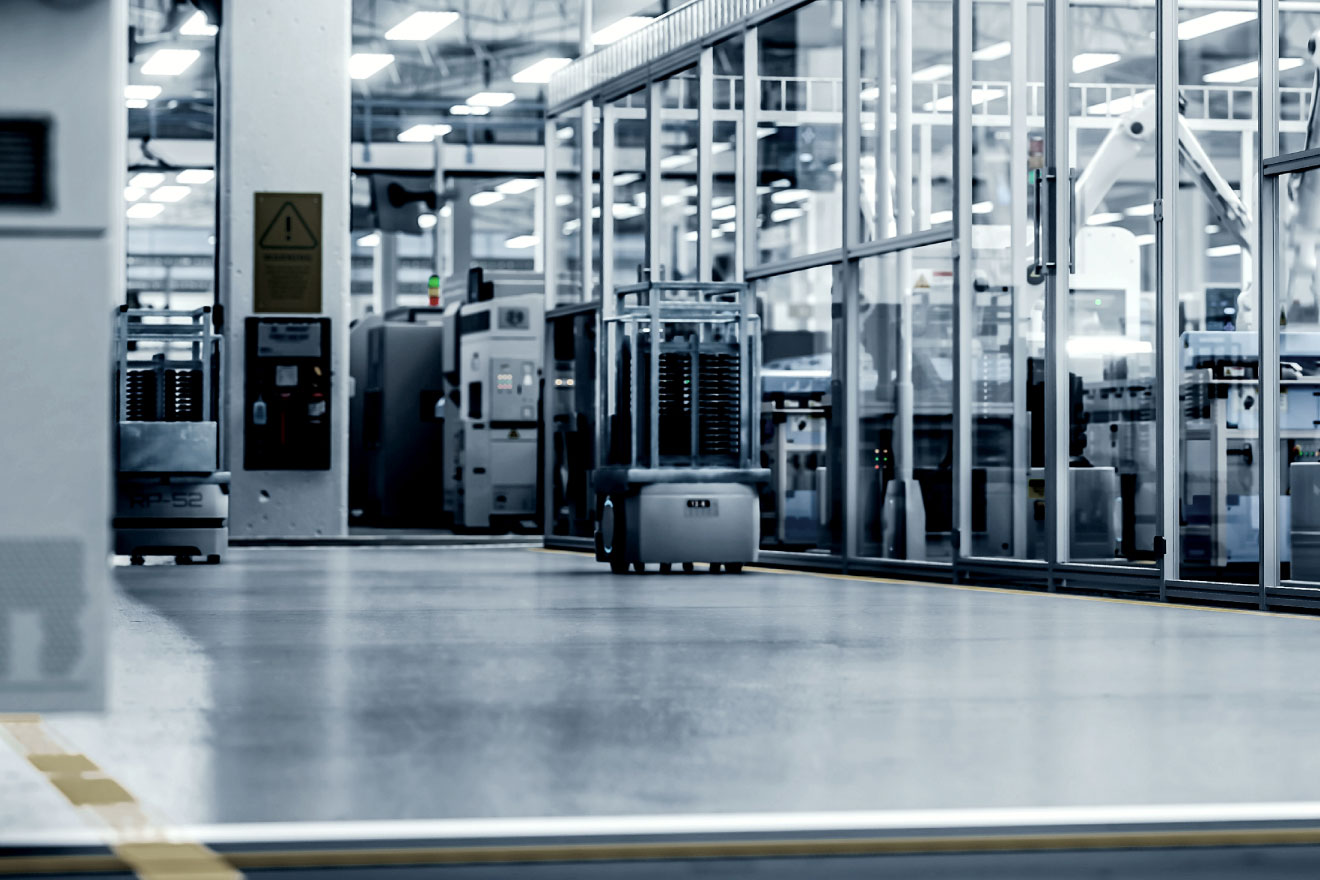
In recent years, labor shortages and rising labor costs in the manufacturing industry have accelerated adoption of automated guided vehicles (AGVs) and collaborative robots. Hokuto is drawing on expertise in automated production equipment to expand into these new domains in an effort to automate associated manufacturing sites. By fostering coexistence between humans and robots, we can help solve industry-wide challenges while pioneering the future of manufacturing in Japan.